C5-Stock Allocation (IC45)
TIP: This program has access to the iTopia Quick Link feature. For more information, click here.
The C5 - Stock Allocation folder displays the stock allocated to Sales Orders from stock, incoming Purchase Orders (PO's), In-Transits, or Branch Transfers for the Product selected in the Header section. The Stock Allocation folder is used with Order Management only, and this folder displays information from the Manual Allocation Override (OM30) program.
- The list box automatically displays Stock Allocations for the current Product. The list box is only as current as the last Allocation run from OM30. If additional Sales Orders, Direct Bills, Credit Notes, Purchase Orders, In-Transits, or Warehouse Transfers are processed after the last Allocation but before the next Allocation is executed, the new information is not reflected in the list box. Lines displayed in Red indicate that there is no stock to allocated the product to.
The following list defines each column in the list box:
- Sales Order - the Sales Order number and the line number.
- Order Type - the Type of Sales Order. Valid options include: Regular, FOB, Sample, Component, Estimate or Draw.
- Customer - the Customer code entered on the Sales Order.
- SO Req Ship - the Required Date on the Sales Order LESS the 'Days to Pick and Pack' from Sales Offices and Warehouses (CC96) LESS the 'Zone' days from Customer Support Masters (SU09/Warehouse/Zone); excluding weekends AND holidays set up in Calendars (md_calendar) view for the current sales office.
- Rec'pt Date - the Receipt Date is the 'Expected Date' from the detail line in Purchase Order Entry (PO40) or the 'Expectant Date' from P/O Receipt and In Transit Entry (PO60) PLUS the 'Receipt Processing Days' from Company Control Initialization (CC00/Purchasing); excluding weekends and holidays from the Calendars view.
- SO Last Ship - Sales Order Last Ship date is the 'Cancellation Date' from Sales Order LESS the 'Days to Pick and Pack' from CC96 LESS the 'Zone' days from SU09, excluding weekends and holidays from CC13.
- Ordered - the Order Quantity from the Sales Order.
- Allocated - the quantity allocated to the Sales Order from the source indicated.
- Guaranteed - the quantity that is guaranteed for the order line. This quantity may come from a PO, In-Transit, Warehouse Transfer or from stock (if available).
- Comp Alloc - the Component Allocation for an Assembled Set. This field displays information only when the Assembled Set is built from Components.
- Stock - indicates whether the units are allocated from stock or not. A Y indicates the units are from stock; an N
indicates that there is not enough stock or that stock may be available from another source. If the stock is available from another source, the PO No, In-Transit or Transfer columns display the source.
- PO No. - the Purchase Order and PO line number from PO40 for the current Product.
- In-Transit - the Receipt and line number from PO60 for the current Product.
- Transfer - the Sales Order, line number and document number (SDN) from Receive Branch Transfers (IC55).
- Customer Name - the Customer Name from the Sales Order.
- Order Priority - the determined priority for the Order. For details on how Order Priority is calculated, click here.
- SO Date - the Sales Order date.
- Earliest Date - the actual Earliest Date from the Sales Order.
- Req'd Date - the actual Required Date.
- Cancel Date - the actual Cancellation Date from the Sales Order.
- To view a snap shot of the Product as of the last Allocation run in OM30, the table below the list box displays the allocated quantity to Stock, on POs, In-Transit and in Transfer. The table also displays whether the Product is On Time (black), Late (blue) or Oversold (red). Note: These statistics do not include Draw type orders.
- For a current view of the Product, the Current section displays:
- On Docs - the total Product count from the documents (Invoices, Credit Notes, Direct Bills, and printed Sales Orders) in Enterprise. This total is dynamic and updates as the documents are created.
- Set B/O - the number of Assembled Sets on back order for this Product. This total is also dynamic and does not require an Allocation run to update. This field displays information only when the Order Management Allocate from Components option is selected in CC00/Order Entry/Order Management Parameters.
- To view the details of the last Allocation run in OM30, the Last Allocation section displays the following information:
- Date and Time - on which the last Allocation was run.
- Run By - the Operator ID that performed that last Allocation.
- On Hand - the Product quantity available as of the last Allocation.
- Avail. for Alloc. - the Product quantity available for Allocation. The Available for Allocation quantity is calculated based on the following formula:
On Hand - On Reserve - WO Res - Sell Hold + (On Res - On Docs)
Note: To view the Availability Forecast screen in IC45, click Go To from the top menu and select Available Forecast from the drop down list.
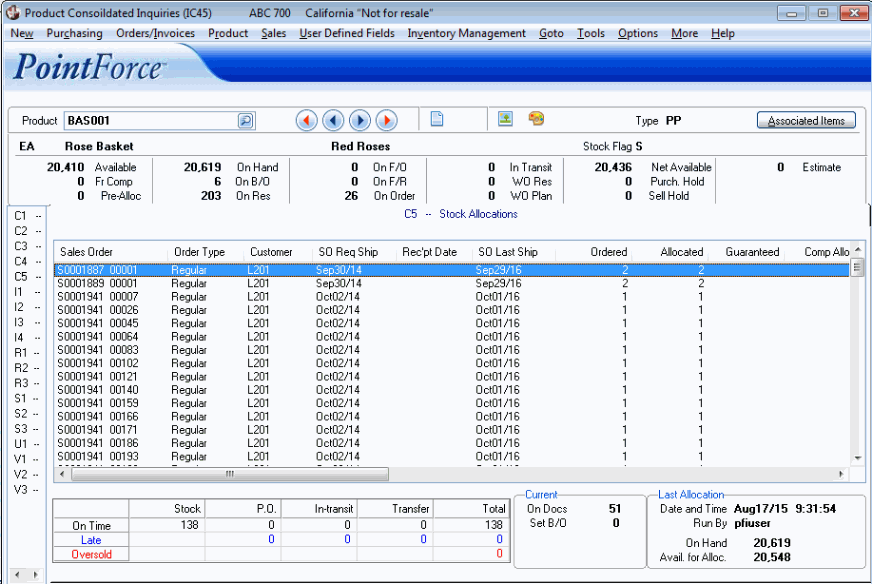
C5 - Stock Allocations
|