Carton Details (PS30)
The Carton Details folder controls the packing of the Sales Orders in Packing Entry (PS30). For additional information on Packing Station functionality, click here.
- Add the Sales Order number:
- If this is the first Sales Order for the Packing Session, scan or enter a Sales Order number in the Sales Order field or the Item Entry field.
TIP: To expedite data entry, the Item Entry field can be used to enter the Packing Number, Sales Order number, Carton ID or Item code. Packers can remain in the Item Entry field and Packing Station automatically places the Packing Number, Sales Order, Carton ID and Item in their respective fields. The cursor automatically defaults to the Item Entry field. For more details on the Item Entry sequence flow, click here.
Note: The first Sales Order entered in Packing Entry
(PS30) establishes the Criteria for the Packing Session. All subsequent Sales Orders for the current session must match the Criteria of this order. Any Sales Orders that do not match the Criteria will be rejected.
Note: You cannot pack draw orders with any other order type.
- When the first order is entered or scanned, the system determines whether the order is a draw order or another type of order.
- If the first order is a draw, then no other order types can be packed in the current packing session.
- If the first order is anything other than a draw order, then a draw order cannot be packed in the current session.
- If this is a subsequent Sales Order:
- Click New Order to clear the Sales Order field and scan or enter the new Sales Order number in the Sales Order field.
OR
- Scan or enter the new Sales Order Number in the Item Entry field.
- Once the Sales Order number is entered, your Packing Number is automatically assigned to this Packing Session. The Packing Number field is in the Header section.
- A Carton ID is required prior to entering items into the Carton. There are 3 ways you can assign a Carton ID:
- Click Create Carton to assign a new system generated Carton ID.
OR
- Scan or enter the existing Carton ID from the Item Entry field. You can print Carton ID labels in Generate/Print Carton ID Labels (PS20).
OR
- In the Carton ID field, scan, enter or select from the Query list the existing Carton ID.
Note: Once the Carton ID field is populated, the Carton Detail grid located below the Carton ID field, automatically populates with the following fields of information if a 'Default Box Type' is set up in Company Control Initialization (CC00/Packing Station):
- Length
- Width
- Height
- Volume
Caution: If the GTIN scanned is flagged as 'Auto PS30 Update' in IM13/PO13, and the Quantity Entry Method is 'Auto', the Length, Width and Height from the GTIN will override the default Box Type value.
- To pack a Carton, ensure you toggle to the Adding Item to Carton
icon.
- To unpack or empty a Carton, toggle to the Removing Items from Carton
icon. For details on unpacking a Carton, click here.
- Scan or enter the item(s) to be packed.
- If you are packing a draw order, you can only pack products that are on the draw order.
- You can under-pack an order; the "un"shipped quantities are returned to the associated estimate order.
- You cannot add products to the pack that are not on the draw. If you want to ship additional products, you must create a new order.
- The following list of products types have unique packing rules. Click on the following links for additional information:
-
The Item Entry Method field indicates the way in which Packing Station is set up to receive this information. The default Item Entry Method setting is determined by the Packer ID defined in Maintain Packing Station Tables (PS09/Packer Identification).
- You can change the default Item Entry Method, depending on your set up in PS09/Packer Identification. If your Packer ID has 'Locked' selected for the Item Entry Method, then you require a Supervisor override to change this field.
- The Item Entry field updates with each scan or entry. The Quantity Entry Method field determines the way in which the entered quantities are updated:
- When the Quantity Entry Method field is set to Auto, the detail line in the list box updates with a pack quantity equal to one (1) for each scan when the Item Entry Method is set to one of the following:
- Product Code
- Customer Product Code
- Sales Order Line number
- Universal (when one of the above is scanned/entered)
- Sales Order Line/Universal (when one of the above is scanned/entered)
When the Quantity Entry Method is set to 'Auto', the detail line in the list box updates based on the SKU Quantity for the GTIN set up for the Product in Maintain Inventory Master (IM13) or in Maintain Purchasing Info (PO13) when the following Item Entry Methods are selected:
- UCC-12 UPC
- EAN/UCC-13
- EAN/UCC-14
- EAN/UCC-8
- Supplier Product Code
- Universal (when one of the above is scanned/entered)
- Sales Order Line/Universal (when one of the above is scanned/entered)
Note: With Carton Control set to Multi Order–Auto, when you are scanning products with GTINs that have a SKU quantity greater than one, a single scan will fill order lines across multiple Sales Orders (that contain the product associated with the GTIN) beginning with the oldest Sales Order. For example, you have 4 Sales Orders that include product 123 (SKU quantity = 5):
- Order Date Nov. 30/08 – Order No. 100127 includes a B/O for product 123 with a b/o qty of 3
- Order Date Nov. 30/08 – Order No. 100130 includes a B/O for product 123 with a b/o qty of 2
- Order Date Nov. 30/08 - Order No. 100123 includes product 123 with an order qty of 1
- Order Date Dec. 02/08 – Order No. 100136 includes product 123 with an order qty of 4
When you scan the product 123 for the first time, Sales Orders 100127 (b/o qty 3) and 100130 (b/o qty 2) will be added to the pack. When you scan product 123 the second time, Sales Orders 100123 (qty 1) and Sales Order 100136 (qty 4) will be added to the pack.
Note:
When the SKU quantity is greater than the Order Quantity and you are able to over pack (Over Shipments in CC00/Packing Station is set to either 'Add to Existing Order Line' or 'Create New Order Line'), the following message displays: "The Pack Quantity of ## is more than the outstanding order quantity of ##. If you wish to pack the additional quantities of this product they will be added to an existing order line with this product if possible, or else added as a new line on the newest order. Do you wish to add the additional quantities of this product? Yes/No".
- Select Yes to add the additional quantities to the Order.
- Select No and the line will not be packed. TIP: If you only want to pack the quantity indicated on the order, either change your Item Entry Method or switch the Quantity Entry Method to Prompt.
If you cannot over ship (Over Shipments is set to 'Not Allowed'), the following message displays: "The Pack Quantity of # cannot be more than the outstanding order quantity of #. Overshipping is not allowed. OK". Click OK to close the message window.
- When the Quantity Entry Method field is set to Prompt, the cursor moves to the Pack Quantity field and you enter the total number of items packed. To update the list box, click on Update Line or press Enter.
A 'touch screen' Number Pad option exists. Using your screen, touch the Number Pad icon, enter the Pack Quantity and touch Enter/Update.
- You can change the default Quantity Entry Method, depending on your set up in PS09/Packer Identification. If your Packer ID has 'Locked' selected for the Quantity Entry Method, then you require a Supervisor override to change this field.
Note: When the Item Entry Method is set to a GTIN type (UCC-12 UPC, EAN/UCC-8, EAN/UCC-13, EAN/UCC-14), Supplier Product Code or to Universal, multiple records can be returned from IM13 and/or PO13 when the GTIN or Supplier Product Code is entered. For more information on the Item Entry Method returning multiple records, click here.
- The Pack Quantity increases as the Outstanding Quantity decreases.
- You can over-pack or under-pack items, depending on availability and depending on the set up of Packing Station (Over Shipments must be set to 'Add to Existing Order Line' or 'Create New Order Line' in CC00/Packing Station or PS10). These exceptions appear as Issues on the Review folder. Depending on the circumstances, Packing Sessions with Issues can be Closed for shipment.
- Note: You can over-pack items beyond the Ship Quantity up to a maximum of the Sales Order's Outstanding Quantity on the current line. When the Over Shipments field is set to 'Create New Order Line', over-packing beyond the Outstanding Quantity requires the entry of a new detail line; an 'A' line is created. When the Over Shipments field is set to 'Add to Existing Order Line', over-packing beyond the Outstanding Quantity results in an addition to the existing Order line if the Product exists on the Sales Order, otherwise a new 'A' line is created.
-
If you are packing a draw order, you can pack a quantity that is less than or equal to the To Ship quantity on the order line of the draw (the "un"shipped quantities are returned to the associated estimate order), but you cannot pack a quantity that is greater than the To Ship quantity. If you want to pack more than the shippable quantity on the draw order, you must create a new order.
- Note: You can short ship items on a draw order. Draws do not accept back orders.
- When all of the items are packed into the Carton(s), review the detail lines in the list box. If a line in the list box is not correct, you can either:
- Highlight the line and modify the Pack Quantity, and then click Update Line.
OR
- Highlight the line and click on Delete Line in order to remove the item(s) from the Carton. You can now repack the item(s) as required.
- If you are tracking Carton Weights and/or Measurements, once each Carton is packed, you have two options:
- The Get Weight button is available when a Scale is defined in PS11. Ensure the Carton ID appears in the 'Carton ID' field and set the actual Carton on the scale. The weight is read in the Measuring Units defined in Maintain Sales Office/Warehouse Number (CC96). The Weight field in the grid flashes yellow twice to confirm the weight. For more details on messages receive from the Scale, see Troubleshooting Carton Details.
- If you are tracking Carton Weight and Measurements, click on Weights/Measures. The Carton Weights and Measurements screen automatically opens for the current Carton ID. For details on using the Carton Weights and Measures screen, click here.
Note: Once a Weight is assigned to the Carton, the 'Weigh Sequence' automatically updates from 9999 to the appropriate Sequence number assigned to the Carton. The Weigh Sequence can be found in the 'Weigh Seq' column in the list box at the bottom of this screen. For more information on Weigh Sequences, click here.
- If you require additional Cartons, repeat from step 3 until your Sales Order is completely packed.
- If you need to empty a Carton: scan, enter or select from the Query list the Carton ID to be 'deleted' and click Empty Carton. For more details on unpacking a Carton, click here.
- If you have additional Sales Orders, repeat from step 1 until all Sales Orders are packed.
- If you need to delete an entire Sales Order: scan, enter or select from the Query list the Sales Order to be deleted and click Delete Order. For more details on deleting a Sales Order, click here.
- When all of the Sales Orders are packed, click on the Review folder to Hold or Close the pack.
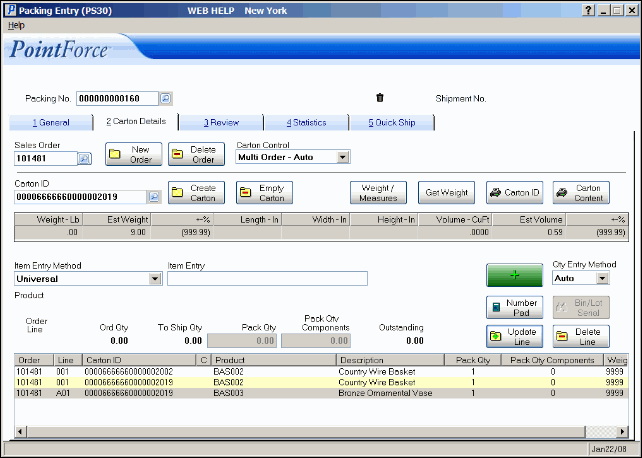
PS30/Carton Details - Adding Items
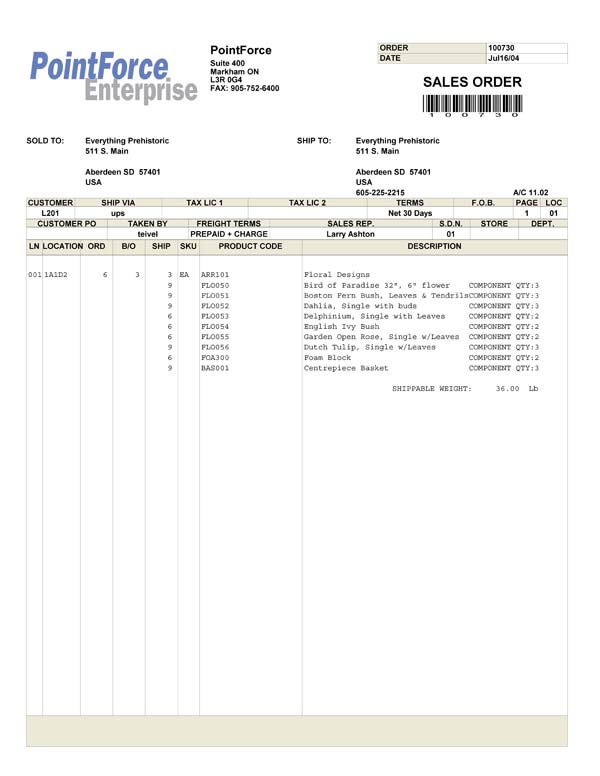
|