The Purchasing Criteria are defined in Maintain Purchasing Tables (PO09) and are assigned to Supplier Product records in Maintain Purchasing Info (PO13/Purchasing). Purchasing Criteria are used to determine when a Product should be reordered. Reorder Quantities (ROQs) are calculated by the system to determine the quantity to be ordered.
The following list defines every field on the PO09/Purchasing Criteria folder:
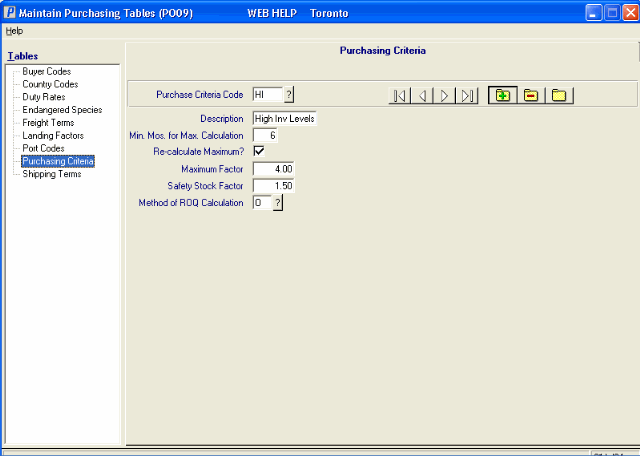
Purchasing Criteria
|