Count Sheet Print (PI08)
The Inventory Count Sheet Printing (PI08) program is used by the Sheet Full and Sheet Partial count methods only. For more information, see Using Physical Inventory.
- PI08 prints Count Sheets for the Products within the range of Count Area(s) specified to be printed. The sequence within each Count Area is defined by the settings selected in Inventory Sort by Bin Location (PI07) (bin location/product, bin location/Supplier Product, just Product code or just Supplier Product Code sequence).
- Note: PI08 only runs for Warehouses flagged for Count Sheet method in Set-up Files for Warehouse (PI01).
- Each new Count Area defined in Physical Count Area Creation (PI04) starts on a new page to allow easy assignment of the Count Sheets to the appropriate count team. Three columns are printed per Product for three separate counts. This is useful for re-counts.
- If the sort includes bin locations, Products that do not have a bin location assigned are printed with a space in the bin location column. They are sorted/printed ahead of any Products that do have a bin location assigned.
- Inventory models (product type = MO) are skipped since we do not expect to have quantity on hand (QOH) for a model.
Note: Under certain circumstances, the following messages are displayed prior to starting the print job:
- "Count records already exist in Count Transaction file. Clear File? Yes/No".
- If there are any records in the Count Transaction file, this message displays. The Count Transaction file can contain all zero-count skeleton records optionally generated by this program, or it can contain real count records entered by the operator via PI12.
- Select Yes to CLEAR all records out of the Count Transaction file and then write new skeleton records for the Products printed on the Count Sheets. Note: If any real counts have been entered via PI12, they will be lost. Select 'Yes' if you have already sorted and printed the Count Sheets but then realized that your sort selection was wrong or a cycle or count area definition was defined incorrectly. If you make your corrections, then re-sort (you must re-sort) and reprint the Count Sheets, then it is appropriate to clear the file first.
- Select No to keep all count records on file. If a Product is printed on a Count Sheet and an existing count record already exists in the Count Transaction file, it is overwritten with a new zero-count skeleton record. Caution:
Select 'No' if you have missed a section of the Warehouse in your original sort/Count Sheet print. For example, your original set up covered bins A000 to A999 and you realized that you must also include bins X000 to X999. You can create a new Count Area for that bin range, re-sort (you must re-sort), and then print Count Sheets for the new Count Area only (enter that Count Area as the Starting/Ending range in program PI08). Counts sheets are printed for the new Count Area only. Skeleton records are added into the Count Transaction file for the new Count Area only; no records are overwritten.
- "***For Lot and Serial Controlled Products ONLY****. Do you want skeleton record written and product reported on Count Sheet if Total Quantity On Hand for the product = 0? Yes - will report the product with a dummy lot/serial number=asterisks. No - will skip the product entirely. Note that if total quantity on hand for a product is greater than zero then the lots/serial numbers with quantity will be listed for counting. Yes/No".
- This message applies to Lot and Serial controlled Products only. If total Quantity on Hand for a Product is not zero, then the lot/serial numbers with quantity are listed for counting. However, if the total Quantity on Hand for the Product is zero, then you have the following options:
- Select Yes to list the Product on the Count Sheet with a dummy lot/serial number (asterisks) on the Count Sheet just in case some stock is found. A skeleton record is written. Note: These dummy count records do not display in the Physical Count Entry (PI12) program. If stock is found, then a new count record needs to be entered with the correct Lot/Serial number(s) recorded.
- Select No to skip printing the Product entirely and to skip writing a skeleton count record. Note: selecting 'No' does not trigger skipping regular Products that have no Quantity on Hand.
Follow these steps to print PI08:
- The Printer Selection screen automatically opens. Select the device destination and click OK.
- The Report Parameters screen for PI08 opens.
- The Report Complete screen opens when the report is generated. Enter the Acceptance Codes to accept the report (if applicable), click Restart to restart the printing of the report, or click Abort to cancel the report.
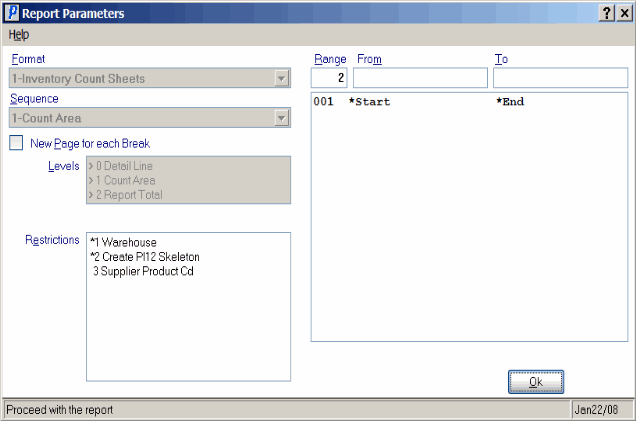
Inventory Count Sheet Printing (PI08)
|