Maintain Cycle Master (PI02)
This program is used by the Tag Partial and Sheet Partial count methods only (see Using Physical Inventory). The Cycle Master Maintenance program is used to define the group of products to be counted in each cycle. Cycles are defined when processing a partial count and you wish to identify only a small section of your warehouse to be counted. A single count cycle can be defined as one of the following:
- Location: defines a starting and ending range of location codes.
- Commodity: defines a starting and ending range of commodity codes.
- Product: defines a starting and ending range of product codes.
If you define multiple cycles, their definition is independent from each other. One cycle could be a range of product codes and another a range of bin locations. The key to each cycle is a unique Year + Count No assignment. These two codes are subsequently used in program PI04 Count Area Creation when defining count areas. A count area could, in fact, be made up of a single cycle or a range of cycles, thereby increasing flexibility in identifying exactly which products or warehouse sections are to be counted. Note: In a full count, because you are counting all products, it is not necessary to define a count cycle that in turn defines a range of locations, commodities, or products to be counted. Simply skip program PI02 and in program PI04 Count Area Creation, define the count area as a range of beginning and ending location codes. If you don't have bin location codes assigned just define the range of bins as [blanks] to ZZZZZZZZ.
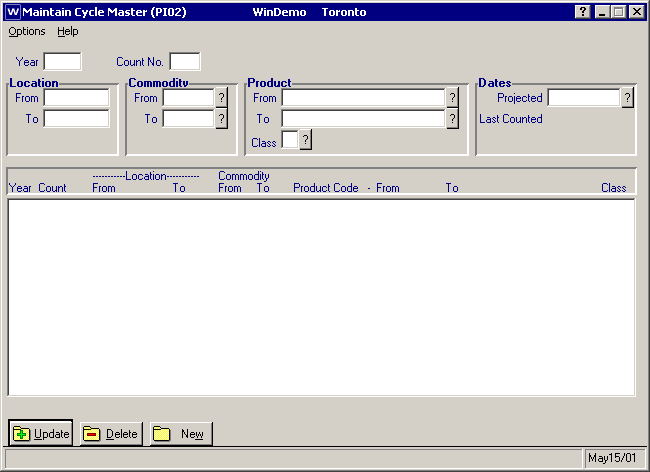
Year
This is a four character (alphanumeric) code that, when combined with the Count No code, becomes the key to each count cycle. There are numerous ways to use this code when defining count cycles. Originally designed to hold the actual calendar or fiscal year each count takes place, some users have created their own coding system to define each count. Some users who cycle count 100% of their inventory every three months, use a two digit year number and the appropriate quarter they are counting. For example, the Year code would look like "02Q3", 02 for fiscal year 2002, and Q3 for the third quarter of the fiscal year. Another way to structure this code is to define the first two characters as the fiscal year, say 02, and the last two characters as the period number, say 09. The resulting Year code then is "0209", representing the 9th month in year 2002.
Count No.
This is a three character (alphanumeric) code that, when combined with the Year code, becomes part of the key to each count cycle. When performing a cycle count, you are typically defining smaller areas to count within the warehouse. Each one of these definitions requires a unique Year + Count No. code combination. Recall that you can format the Year field in several different ways. If you decide to format Year as the current fiscal year, say "2002", and you just want to increment Count No. by 1 for each new cycle count definition, then you could use a Count No. of "001", "002", "003", etc. On the other hand, you might want to define the month and then the count within the month. For instance, Count No. "A01" is the first month, first count; "A02" is the first month, second count; "B03" is the second month, third count. If you format Year as fiscal year and quarter (e.g. 02Q3), you may simply want to use a simple sequential numbering system ("001", "002", "003", etc.) in Count No. to define the counts that fall under each fiscal/quarter period. If you format Year as fiscal year and period (e.g. 0209), the Count No. might best be defined by the actual day the count is to take place (e.g. day "105", "106", "107", etc.). Some organizations cycle count every day, so this method might be best.
As you can see, the objective here is to use a unique coding structure that makes sense under your environment. The examples given here are only to illustrate the flexibility of the Cycle Count system. Note: In the final step of the physical count, program PI19 posts adjustments for the count variances and then clears the temporary Physical Inventory files except
for the cycle definitions. They are only cleared if the user recalls a cycle and deletes it manually.
Location
From The beginning location code used to define this count cycle. Note there is no input validation on this field. For instance, if you wished to count all products between locations starting with the letter "A" up to and including locations beginning with "D", the starting location would simply be "A" (the first possible location starting with the letter "A")
To The ending location code used to define this count cycle. Note there is no input validation on this field. For instance, if you wished to count all products between locations starting with the letter "A" up to and including locations beginning with "D", the ending location would be "DZZZZZZZ" (the last possible location before the first "E" location)
Commodity
From The beginning commodity code used to define this count cycle. This value is validated against the Commodity Code master file.
To The ending commodity code used to define this count cycle. This value is validated against the Commodity Code master file.
Product
From The beginning product code used to define this count cycle. This value is validated against the Product master file.
To The ending product code used to define this count cycle. This value is validated against the Product master file.
Class The product class code for the products just defined in the From and To fields above. This is a further "filter" within the given product range. For instance, if you selected products from "000001" through to "009999", and then selected class "A", you would only be counting products that have a class code "A" within the given range. A wildcard value of "*" does not restrict the product code range to class.
Dates
Projected This is a date field, used to tag each cycle count record with your anticipated count date. The Projected field initially defaults to the current system run date.
Last Counted This is a memo date field that identifies the date this count area was counted, as updated with the PI19 Transfer Physical to Book program update routine.
Options Menu
PI02 works with warehouse restrictions. Upon entry into PI02, the operator's default warehouse is selected. Note: prior to maintaining the count cycles, ensure you are in the correct warehouse! In multi-warehouse environments, you must use the Options Menu to change your warehouse selection.
|