The CC00/Inventory Control folder defines the parameters that effect the Inventory Control (IC) system.
The following list defines every field on the Inventory Control folder:
- In the Rounding Rules section:
Rounding Rules apply to the Recalculate Selling Prices (IM28) program that recalculates Selling Prices. The Rounding Rules for this recalculation program are defined here in CC00/Inventory Control.
The Inventory Rounding Rules feature can be divided into two areas:
- What price ranges of product should have which rules applied? These values are entered in the For Prices Below and Round to Nearest input fields.
- How should the Selling Prices be rounded? There are three options:
- Round Up - always round up to the target defined in Round to Nearest.
- Round Down - always round down to the target defined in Round to Nearest.
- Split - round up for values greater than half of the Round to Nearest target and round down for values less than half of the Round to Nearest target.
For example, a Product has a Selling Price of $9.57. The associated Rounding Rule is 'For Prices Below' 100.00 round to the nearest 0.10.
- If Round Up is selected, this example results in a Selling Price rounded to $9.60.
- If Round Down is selected, this example results in a Selling Price rounded to $9.50.
- If Split is selected, this example results in a Selling Price rounded to $9.60 (9.55 through 9.59 would be rounded up, while 9.50 through 9.54 would be rounded down).
For Prices Below - the 'For Prices Below' input fields, in conjunction with the 'Round to Nearest' input fields, provide the ability to define various ranges of Selling Prices with different rounding rules. Each line in conjunction with the line below on the table represents a range of selling prices. For example:
Round to Nearest - the 'For Prices Below' input fields, in conjunction with the Round to Nearest input fields, give the ability to define ranges of selling prices and round each differently when recalculating selling prices. Each line on the table represents a range of selling prices and the rounding target to be used for each.
- When IM28 is executed, the resulting prices are checked against this table. The value in the Round to Nearest input field is used as a target to ensure that all selling prices generated will conform to the appropriate target.
- For example, a distributor may decide that inexpensive items should be priced as accurately as possible, and therefore choose to round these items to the nearest penny. Conversely, expensive equipment may need only to be rounded to the nearest dollar so that customers would see prices in whole dollars.
- The Round to Nearest input field is used to set the target format for the selling price generated by program IM28.
Desired Outcome: |
Enter: |
To Disable rounding (force Enterprise to price
accurately to the penny) |
0.01 |
To force selling prices to the nearest quarter |
0.25 |
To force selling prices to the nearest 50 cents |
0.50 |
To force selling prices to the nearest dollar |
1.00 |
-
The range of prices to which this 'target' applies is determined by prices entered in the For Prices Below input fields.
- Stock Depletion Classification - BACKGROUND: each inventory item created in Enterprise through IM13 is assigned a class code. Class codes are created in Maintain Inventory Tables (IM09/ABC Class Codes), and are used by Enterprise's purchasing system and its inventory reporting programs.
- Based on the 'dollar value demand' of inventory items, Report/Reset Class Codes (IM61) will reclassify all inventory items into descending order; therefore, products with the highest dollar value demand will be at the top of the listing and in the highest classification. The classification is a single character alphabetic code with allowable classifications being A through L. A is the highest classification, which will be given to products with the highest dollar value demand by running program IM61.
- The Stock Depletion Classification field is used to control for which products a stock depletion check will be performed during certain circumstances in the Order Entry and Invoicing programs. The class entered into this field in CC00 represents the lowest product class for which the stock depletion check is desired.
- In Enter Orders/Quotes (OE30), and in Enter Inv/Direct Bills/Credits (IN41), a stock depletion check will be performed if the current product has been defined as a Stock product in IM13/Stock, and if its Class Code is equal to or greater than the class entered here in CC00.
- For example, an entry of class C in this field will cause the stock depletion check to be performed for all 'stock' products having a class of A, B, or C.
- The stock depletion check will cause a warning message to appear during Order Entry in OE30, or during Invoice Entry or Direct Bill entry in IN41 (Enter Invoices Direct Bills and Credits) if the quantity placed on the order causes the product's available stock to fall beneath the Minimum Quantity set up in IM13/Warehouse by at least one half of that minimum.
- For example, Product ABC has a minimum quantity of 50, and there are currently 75 pieces of this product in the warehouse.
- When an order for 60 is entered for this item, the available quantity will fall to 15 pieces, which is less than half of the minimum of 50.
- The purpose of this warning message is to immediately identify to customer service people, or warehouse staff that an item has fallen below the minimum quantity, and that a significant portion of that minimum (also known as Safety Stock) has already been allocated to customer orders. Because this message appears, the person entering the order or invoicing the delivery is now able to call the attention of the purchasing agent to this potentially low stock level, and thus perhaps avoid stock-outs on this product.
Caution:
It is not advantageous to force this message to appear every time a product's available quantity falls below this level. Operators who see the same reoccurring message too frequently are likely not to give the message any importance. By selecting a higher classification for this check/message, the operator will only be presented with the warning for products where it makes sense to draw someone's attention to the situation.
Note: This check is not performed in program RS41 (Enter Cash Counter Invoices).
- Color Separator - enter the single character used to separate the Product code from the Color/Size code.
Products which are identical one to the other with the exception of a single characteristic such as color or size can be identified in Enterprise as "common products". These products share a product code, but are identified with a unique suffix at the end of the part number.
- Here are some examples:
1000-BLUE |
1000#01 |
1000^S |
1000-RED |
1000#02 |
1000^M |
1000-BLACK |
1000#03 |
1000^L |
1000-GREEN |
1000#04 |
1000^XL |
- The following characters cannot be entered in the color separator field:
- Letters A through Z
- Numbers 0 through 9
- Characters / and \
- Note: You can alter the color separator in CC00 until the first product is entered in IM13. Once a product is entered in IM13, you cannot change the color separator.
- Lot Control - when selected, this option enables the Lot Control features within Enterprise. Special lot control features are enabled in transaction programs for products which are identified as Lot Controlled in IM13/Stock. These special features allow the recording and monitoring of individual "lots" of product within a single product code.
- A product which is not Lot number controlled would be displayed as follows in inventory displays and reports:
Product |
On Hand Qty |
|
1500 |
20 EA |
|
- This product is Lot Controlled, and as such, Lot numbers are displayed on queries and reports:
Product |
On Hand Qty |
Lot Number |
1500 |
20 EA |
3892 |
|
22 EA |
3894 |
|
8 EA |
3897 |
Total: |
50 EA |
|
-
A "lot" may contain one or more items within a single Product code. Products which are produced in batches and which can be date sensitive are often lot controlled for quality assurance purposes (e.g. Pharmaceuticals, Paints, Chemicals).
- This option cannot be disabled when Lot transactions are currently on file.
- Serial Numbers - when selected, this option enables the Serial Number Control features within Enterprise. Special Serial Number control features are enabled in transaction programs for products which are identified as Serial Number controlled in their product master file (as maintained in program IM13/Stock - Maintain Inventory Master). These special features allow the recording and monitoring of individual "serial numbers" of product within a single product code.
- A product which is not serial number controlled is displayed as follows in inventory displays and reports:
Product |
On Hand Qty |
|
1500 |
4 EA |
|
- A product that is Serial Number Controlled is displayed on queries and reports with the Serial Number:
Product |
On Hand Qty |
Serial Number |
1500 |
1 EA |
1A253 |
|
1 EA |
1A254 |
|
1 EA |
1A255 |
Total: |
3 EA |
|
- A single serial number may only be used once with a single product code. Products which are expensive, have electronic components, or are manufactured are often Serial Number Controlled (e.g. Computers, Cameras, Engines).
- Assortment Pricing - an Assortment represents a series of products (SKU's) that belong to the same family. You can decide, regardless of the number of individual SKU's purchased, to group these products together as if they are purchased against a single SKU to obtain the better quantity price break. The total quantities of products that share a common assortment code will be added together and the applicable detail lines re-priced based on the accumulated amount.
- Assortment Pricing is assigned to the Product using the 'Assortment Pricing Code' in IM13/Selling.
- Use Second Description - products created in IM13 must be described with a Primary Description, but can optionally be described with an additional Secondary Description.
- When selected, this field enables the printing of this Secondary Description on the following reports:
- This description will be displayed on queries and displays if space on the screen permits.
-
This option can be activated or de-activated at any time without program consequences, however, consistency in forms printing will be affected.
- Freight Rev. - Satellite Whse - when selected, the freight charge applied to Warehouse transfers is reversed when the transfer is updated through Receive Branch Transfers (IC55) and Whse Receipt Stock Audit Trail (IC56). The cost of the Product is not increased or decreased if the Product is returned to the main Warehouse or transferred to a Satellite Warehouse.
- For example:
- Warehouse '01' is Toronto and it is the main Warehouse.
- Warehouse '02' is Montreal and is a Satellite Warehouse.
- Warehouse '03' is Vancouver and is also a Satellite Warehouse.
- IM09/Warehouse Shipping Rates: 10% add-on to send Product to Montreal; 15% add-on to send Product to Vancouver from the central Toronto Warehouse.
- If an item has a Toronto cost of $10.00 and is sent from Toronto to Montreal, the resulting cost is $11.00 (10.00 + 10%). If the item is sent from Toronto to Vancouver, the resulting cost is $11.50 (10.00 + 15%).
- If the item is returned from Montreal to Toronto, the freight is backed out. The $11.00 item that is shipped from Montreal (satellite) back to the Toronto (central) Warehouse arrives back at Toronto at $10.00.
- If the item is sent from one satellite (Montreal) to another (Vancouver), the system will treat it, for cost purposes, as though the item has been returned to the central Warehouse (Toronto) and then shipped to the other satellite. Therefore, the costing goes from $11.00 in Montreal to $11.50 in Vancouver (11.00 minus 10% plus 15% = 11.50).
When this flag is not selected, transfers through IC55 and IC56 will not reverse the freight charges during Warehouse transfers.
- Model Cost Rollup - allows you to rollup the selling price of a model header based on the calculated selling price of the components (fixed or variable). This option is designed for use with active price lists based on Markup on Cost or Gross Margin only. When selected:
- The selling price of the model header is disregarded.
- The selling prices of the components of the model are rolled up to the model header regardless of whether the components are variable or fixed.
- Once a selling price is determined, best price logic will determine the best price for the model. For example, if there is a better price for the model on another price list, the rolled up price will be disregarded and the best price for the model header will be used as the selling price.
There are a number of different scenarios based on the type of model you are using. For more details, please see the Model Cost Rollup Examples topic.
- Product Label Format - this field works with Print Product Labels (IM42). Enter or select from the query a Product Label Format; the Format selected here becomes the default Product Label Format in IM42.
Note: You can change the default setting in IM42.
- Default Price List
- enter or select from the query the Default Price List to be used as the Default Master Price List with the following programs:
- IM42 - printing Product labels that include a price.
- IM13 - the Default Price list on the 'Pricing' folder.
- SU13 - the Default Price list on the 'Pricing' folder.
You can change the Price List in IM42, depending on the type of label selected. You can also change the Price List in IM13 and SU13.
Note: Only Price Lists set up in Domestic currency can be selected.
- Special Product Mask - this field dictates the structure of the Product code when Special Products are created within the Order Entry, Invoicing, Purchase Order Entry, and Quick Product Creation programs. The mask assigned should consist of the following:
- 1 or more leading characters - entry of this character(s) in the programs mentioned above will trigger creation of a new product on the spot in the originating entry program.
- A series of '#' which will be replaced by the next available number.
- Any suffix to complete the format to the maximum number of characters in a Product code.
- Mask "9####-00" will generate product codes 90001-00 to 99999-00.
- Mask "ZZ###### will generate product codes ZZ000001 to ZZ999999.
For more information on special products, see the About Special Products topic.
- Last Special No Used - the last "special product" part number that has been generated by Enterprise according to the "special product mask" defined in CC00/Inventory Control will be displayed in this field. Enterprise will display the generated number portion only of the special product code; any mask or other formatting applied will not be displayed.
For example:
Mask: |
ZZZZ######## |
|
Last Number Used: |
ZZZZ00000368 |
|
Displayed: |
00000368 |
|
This is memo information only and cannot be entered or altered.
- Main Warehouse - this field is used to identify the central warehouse or main distribution point within the list of sales offices/warehouses. It is important to identify the Main Warehouse correctly, as Enterprise can be used to automatically replenish inventory levels in the primary and in the secondary warehouses. Although the procedure is quite similar for all locations, different programs are used to bring stock into the main warehouse than are used to replenish inventory into the secondary warehouses.
- Only a single warehouse can be designated the "Main" warehouse. This warehouse must have been previously created in Maintain Sales Office/Warehouse Numbers (CC96).
- A business with a single location would normally enter the warehouse number into this field, and leave the secondary warehouse field blank. A business with multiple locations would normally enter the number of the main or central hub into this field, then enter all secondary warehouse locations into the Secondary Warehouse field.
- You can change the Main Warehouse if desired. When you select a different warehouse, the following message displays: "The main warehouse is being changed from XX to YY. Do you want this to occur? Yes/No".
- Select No to close the window and the current warehouse remains the Main Warehouse.
- Select Yes to replace the current main warehouse with the selected warehouse. The previous main warehouse selection is moved to the end of the Secondary Warehouses chain.
- When products are set up in IM13, the system defaults to the main warehouse on the IM13/Warehouse folder. If you change the main warehouse in CC00, the warehouse for the product in IM13/Warehouse will not change, but the Main Warehouse check box will be automatically de-selected.
- If you change the main warehouse, a Branch Warehouse Record (ICWM) is created for each product for the new main warehouse if one does not exist.
- Secondary Warehouses - this field is used to list all of the secondary warehouses operated by a company. The warehouse numbers should be entered into this field as a 'string' without separating spaces or characters (eg. 02030405 – representing warehouses 02 and 03 and 04 and 05).
- You cannot add the main warehouse to the secondary warehouse string.
- You can remove warehouses that have no inventory activity; warehouse(s) with inventory activity cannot be removed.
- The maximum number of secondary warehouses you can enter is 18.
- All warehouses entered must already exist in CC96.
- Cost Calculation Method Using On Hand Balance - if either Lot or Serial Number Control is used by your company, then Enterprise must calculate average costs based on warehouse, not company-wide costing rules. This is set up by your Enterprise Business Consultant.
- Last Used UPC Counter - this field displays a count of the UPC Codes generated through IM13/Pack Info and PO13/Pack info.
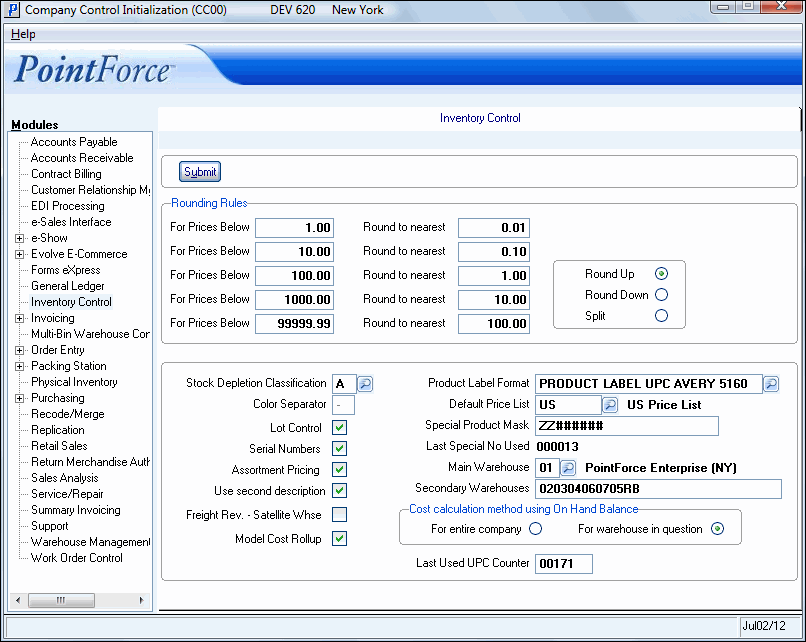
Inventory Control (CC00/Inventory Control)
|