Warehouse Folder (IM13)
The Warehouse folder contains details on the re-stocking and replenishing of the Product selected in the Header record. Bin locations can also be tracked on this folder.
Note: When you make changes to the information on the Warehouse folder, you must click on the Update button on the folder itself in order to have the changes take effect. The Update button is in the bottom left corner of the folder and activates only when changes are made.
The list below defines every field on the Warehouse folder:
- Warehouse - enter or select from the Query the Warehouse Code in which this product is kept.
- Main Warehouse - checkbox indicates that the Warehouse is the main or primary Warehouse. The checkbox is automatically selected for Warehouse defined as a Main Warehouse in Company Control Initialization (CC00/Inventory Control).
- When the checkbox is not selected, the Warehouse is a Secondary Warehouse. Secondary Warehouses are usually only single-bin, unless the Secondary Warehouse is set up as a Multi-Bin Warehouse in CC00/Multi-Bin Warehouse.
Bin Locations:
- Bin Locations represent physical locations in the Warehouse. These locations may be coded to signify a precise location, for example you may use a combination of area + aisle + shelf + bin.
When following the standard set up, the Main Warehouse has two Bin Location codes: Primary and Secondary; and the Secondary Warehouse(s) has only one Bin Location code: Primary. If you are using the Multi-Bin Warehousing feature, the Primary and Secondary Bin Location fields are unavailable. Products are assigned to locations using a separate sub-system in a Multi-Bin environment.
- Primary - identifies the primary location of the product in the Warehouse. This code can be a maximum of eight alpha-numeric characters in length.
- When the Picking Sequence Flag on the CC00/Order Entry screen is set to L (Location), the detail lines on the Picking Slip will be sorted by the Primary Bin location.
- Secondary - identifies an alternative location of a product within the Main Warehouse only. This code can be a maximum of eight alpha-numeric characters in length.
- The Secondary location is most commonly the 'overflow' stock area in the Warehouse.
Note: Both bin locations may be listed on various reports, including Print Inventory Listing (IM15) and Print Inventory Evaluation (IC81).
Restocking Info:
- Reorder Point - is the quantity at which re-purchasing should occur. The Reorder Point can be manually entered and maintained or once the product has accumulated sufficient history, the Reorder Point value may be calculated and reset automatically using Forecast, Purchasing, Lead-time Recalculation
process (PO25/26).
- When the Automatic Purchase Order generation routines are running, any product with a net available quantity below the Reorder Point (also known as Order Point) will trigger a Purchase Order.
- When printing the Reorder Report (PO20), the report may optionally be restricted to printing only those products whose quantity available has fallen below the Reorder Point (ROP), which highlights products that require immediate purchasing attention.
- Reorder Qty - is the suggested reorder quantity. The Reorder Quantity can be manually entered and maintained or the Reorder Quantity may be recalculated and reset automatically using the PO25/26 process.
- Reorder Quantities are calculated based on a combination of the Purchase Criteria (from Maintain Purchasing Info PO13) and the Forecast usage. Both values may be calculated by the PO25/26 process; the Maintain Forecast Calculation Codes (PO07) and Maintain Purchasing Tables (PO09/Purchasing Criteria) are maintained in order to define how Forecast and Purchase Criteria are calculated by the process.
- The Reorder Quantity is a value reported on the Reorder Report (PO20).
- Line Point - is the inventory level that triggers a Purchase Order if a Supplier is on a cyclical review (i.e. cycle in days is set for the supplier in PO11). The Line Point inventory level is greater than the Reorder Point level by the quantity forecast during the review cycle. The Line Point value can be manually entered and maintained or may be calculated and reset automatically using the PO25/26 process.
- Minimum Quantity - is the minimum desired stock level. The Minimum Quantity can be manually entered and maintained or once the product has accumulated sufficient history, the Minimum Quantity may be calculated and reset automatically using the PO25/26 process. The Minimum Quantity cannot be greater than the Maximum Quantity for the product.
- The Minimum Quantity is equivalent to the Safety Stock level. This value prints on the Reorder Report (PO20).
Additionally, this value is used by the Stock Depletion test performed during Order Entry and Invoicing. If the order quantity entered will deplete the stock level to 50% of its Minimum Quantity, a warning will be given to the operator (for products within the class code range specified).
- Note: All products require a Safety Stock level. During normal operations, Safety Stock is not used to fill orders; it is purchased as insurance against the possibility of unanticipated demand, abnormally long lead times, transportation strikes, etc. Sufficient Safety Stock levels should be maintained to prevent stock-out costs (i.e. the cost of "lost" sales); however, Safety Stock levels should not be so high that inventory carrying costs are over-burdened.
- Maximum Quantity - is the desired maximum stock level. The Maximum Quantity can be manually entered and maintained or once the product has accumulated sufficient history, the Maximum Quantity may be calculated and reset using the PO25/26 process. The Maximum Quantity cannot be less than the Minimum Quantity for the product.
- The automatic recalculation of the Maximum Quantity for a product by the PO25/26 process may be prevented by disabling the Recalculate Maximum
field on PO09/Purchasing Criteria.
- The Maximum Quantity value is used by the ROQ Order Up To Maximum method (Re-Order Quantity). The Method of ROQ Calculation is set in PO09/Purchase Criteria.
- Monthly Forecast - stores the monthly Forecast Usage (in SKU's). The value can be manually entered and maintained or once the product has accumulated sufficient history, the value may be calculated and reset using the PO25/26 process. Weighting factors established by the Forecast Calculation are applied to the monthly demand units maintained for the product.
- Note: The Forecast should be calculated and maintained on a monthly basis to reflect the changing trends of the product's requirements.
Bin/Location Replenishment:
- Replenishment Point - this field is available only when a Multi-Bin Warehouse is entered in the Warehouse field. The Replenishment Point is the point at which additional product needs to be added to the Primary location or Pick Area for the product.
- Pick Area Max Qty - this field is available only when a Multi-Bin Warehouse is entered in the Warehouse field. The Pick Area Maximum Quantity is the desired maximum stock level for this product in the Pick Area of the Warehouse. The Suggested Putaway and Replenishment (WH81) program uses this entry to automatically invoke the replenishment of the bins.
Note: When you make changes to the information on the Warehouse folder, you must click on the Update button on the folder itself in order to have the changes take effect. The Update button is in the bottom left corner of the folder and activates only when changes are made.
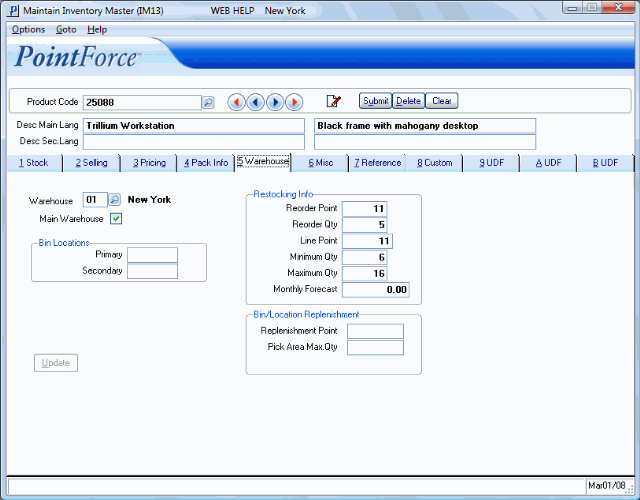
IM13/Warehouse Folder
|