WO Example
We will be working with an example of a Work Order product with the following specifications:
The set of 5 Ink Jet Cartridges (2 black, 1 red, 1 blue, 1 yellow) will be sent to the Cartridge Supplier (CARSUP) for packaging. The cartridges will be boxed together in a pre-printed cardboard box that is produced and stocked by CARSUP, and we have negotiated a price of $1.50 to supply the printed box and the labour to package this for us.
PO13 Set Up:
PO13 must be used to link the Work Order Product to the appropriate Supplier. It also defines the Purchase Price and any applicable Landing Factors for the WO product. If you build the products yourself, then you must first define your own organization as a supplier in PO11, then link all these products to that supplier code.
We'll be working with the following example from PO13:
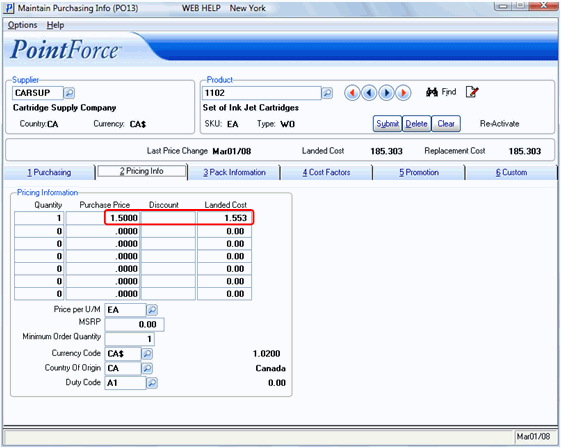
Set up for PO13/Pricing Info folder
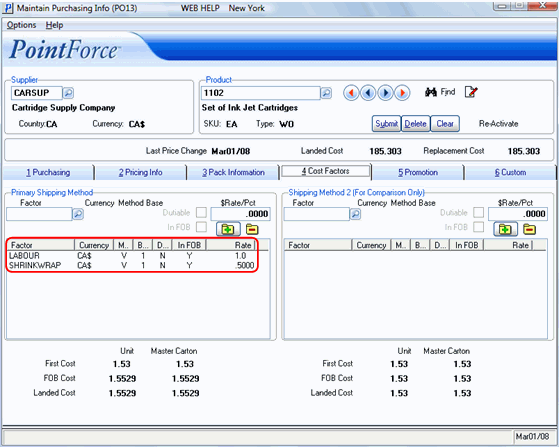
Set up for PO13/Cost Factors folder
The specific PO13 fields that are relevant for the WO system include:
- Purchase Price - on the Pricing Info folder, the Purchase Price field is used to define your cost (in appropriate currency) for any work to be performed or product enhancements to the final Work Order product by the supplier to your WO product prior to receiving into your warehouse. Remember the this is the TOTAL charge for all the work (and material) the Supplier will bill you for working on the product. Note: This price may be overridden in PO40 if needed.
Example: The set of 5 Ink Jet Cartridges (2 black, 1 red, 1 blue, 1 yellow) will be sent to the Cartridge Supplier (CARSUP) for packaging. The cartridges will be boxed together in a pre-printed cardboard stock that is produced and stocked by CARSUP, and we have negotiated a price of $1.50 to supply the printed box and the labour to package this for us.
- Landing Factors - on the Cost Factors folder, the Landing Factors are used to assign the appropriate labour or item costs to your WO product that will be applied to the total WO product costs once the items are received via PO60.
Example: The cost to you to shrink wrap the boxed set of Ink Jet Cartridges is $1.00 per unit and the cost of Shrink wrap is estimated at 50 cents per unit. Therefore these two Landing Factors have been previously defined in PO09/Landing Factors to accommodate these charges. Note: These charges should reflect the TOTAL charges incurred to produce one SKU unit. The WO13 program will automatically multiply these costs by the Planned Quantity (see the 'WO13 Set Up' section below for further details on this feature).
Note on Landing Factors
It is recommended that your PO13 Landing Factors be set up on a Unit basis to accommodate the unit (fixed unit) price assignment for these costs in PO13. In this example, we are choosing to identify the Shrink Wrap as a factor which does not track inventory. Another user may decide to add the Shrink Wrap as a component against the Work Order Product via WO13. This example is used to illustrate the flexibility in the system.
WO13 Set Up:
WO13 is the key to the Work Order system. WO13 is where the 'WO' products previously maintained in IM13 are assgined all the components and build instructions/notes. It also displays the costs for the WO product, dynamically updated as components and planned quantities are maintained.
Here is an example of the WO set up for product 1102:
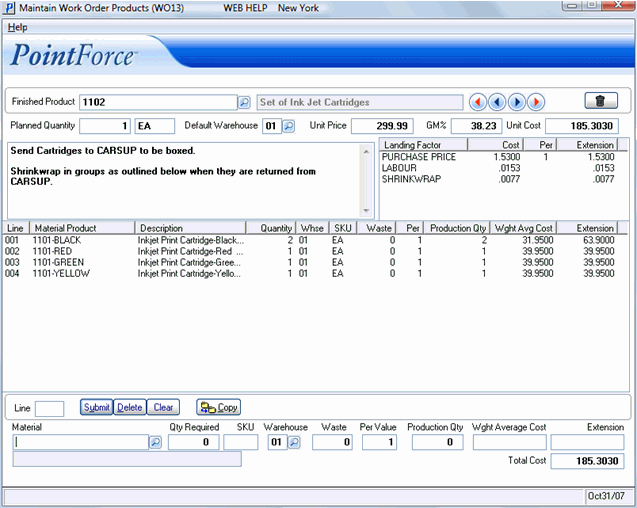
Set up for WO13
|