The Suggested Putaway and Replenishment (WH81) program allows you to print two reports that can aid you in determining which bins the product should be relocated to using the Whse Relocate Stock (WH30) program.
The following describes the reports that you can obtain through WH81.
- Suggested Putaway Report lists products received through the Enter Receipts/In-Transits (PO60) and Receive In-Transit to Stock (PO63) programs that that were received into the ‘General’ receiving bin.
Once the acceptance codes are entered the reported records are transferred to WH30 for confirmation.
The report contains the following information:
- From Bin/Loc – The original Bin Location the product was received into.
- Bin Type – The Bin Type of the original bin location.
- Product – The Product code.
- Description – The Description of the product.
- Qty to move - The quantity that was received and can be moved to another bin location.
- To Bin/Loc – The suggested put away Bin Location to relocate the product to. Note: If there is no suggested put away bin the product could not be located in any existing bin.
- Type – The Type of the suggested put away bin location.
- The Replenishment Report lists products that can possibly be relocated from one bin to accommodate existing backorders. Data for report will only be produced if the ‘Bin/Location Replenishment’ fields are populated in Maintain Inventory Master (IM13). The data reported is a result of comparing the current inventory for the product in each bin these fields. If the product Bin/Loc available quantity is over the replenishment point the product is not reported. If the product Bin/Loc available quantity is below the replenishment point the product is reported to transfer inventory from a Bulk Bin/Loc to a Prime Bin/Loc for the quantity needed to reach the replenishment maximum.
If the product is lot controlled, WH81 first verifies that the same lot exists in a Bulk location as the Primary location quantity.
Once the acceptance codes are entered the reported records are transferred to WH30 for confirmation.
The report contains the following information:
- From Bin/Loc – The Bin Location the product can currently be relocated from.
- Bin Type – The Bin Type of the that the product is being relocated.
- Product – The Product code.
- Description – The Description of the product.
- Qty to move cases/skus
- The quantity that can be moved to the ‘To Bin/Loc’. The quantity for the Cases is based on the quantity entered in the # Pcs/Selling Unit field of the ‘Maintain Inventory Master (IM13)’ program on the ‘Stock’ folder. For example: If there is a quantity of 40 in the Bulk bin and the # Pcs/Selling Unit is 15 the program divides the total quantity of 40 by 15. The result in this case is 2.66. Only whole units can be relocated, therefore, a quantity of 2 is displayed as the number cases that can be relocated. These 2 cases represent a quantity of 30 units. As a result 10 units is displayed as the sku quantity.
- To Bin/Loc – The suggested put away Bin Location to relocate the product to.
- Type – The Type of the suggested put away bin location.
Once you execute WH81:
- The Printer Selection screen automatically opens. Select the device destination and click OK.
- The Report Parameters screen for WH81 opens.
- When all of the information on the Report Parameters screen is complete, click OK to run the report.
The Report Complete screen opens when the report is generated. Enter the Acceptance Codes to accept the report (if applicable), click OK to complete the printing of the report, or click Abort to cancel the report.
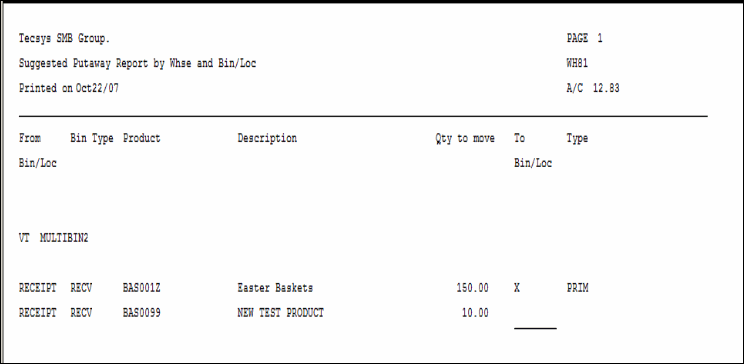
WH81 – Suggested Putaway report example
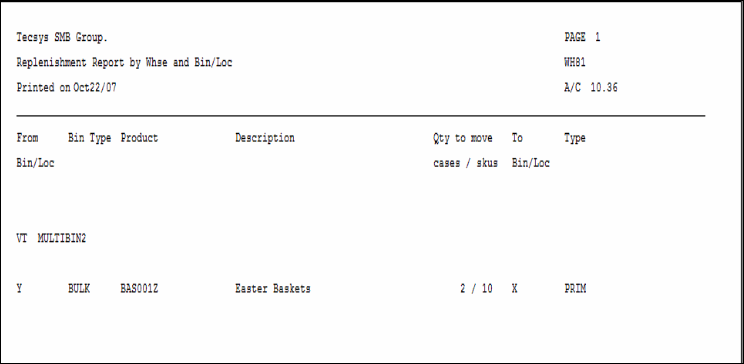
WH81 – Replenishment report example
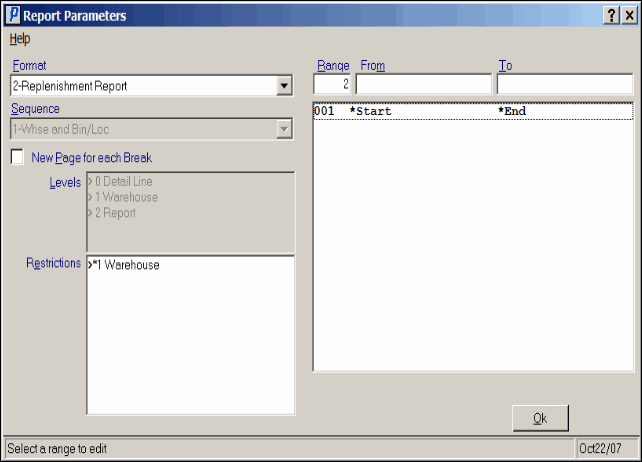
Suggested Putaway and Replenishment (WH81)
|